Our Services
and Facilities
Capabilities: All of our workstations are scaled equally at 30’ deep, 16’ wide and 12’ high and are connected by an overhead track with trolleys. This allows for efficient transfer from step to step.
What is Powder Coat? Powder coating is a type of coating that is applied by electrostatic charging of free-flowing, dry powder. The main difference between a powder coating and conventional liquid paint and is that the powder coating does not require a solvents to keep the binder and filler parts in a liquid suspension form. Once applied, the Powder coating is then cured using heat which allows it to flow and form a "skin". The powder is most commonly a polyester TGIC but may also be a polyester epoxy hybrid, or polyester urethane with each type suited to meeting the end use of the product. It is used to create a hard finish that is tougher than conventional paint. Powder coating is commonly used for coating of metals, such as steel and aluminum.
Assembly: Do you have components that need assembly after powder coating? Let us know. Why pack individual components after coating only to re-queue and unpack for assembly at your facility? We can assemble and pack it once saving time and overall cost. Let's talk!
Blast Room: 30’x16’x12’ high
Utilizing steel media and our 5000 lb capacity hopper, we are able to efficiently remove rust, paint, weld and laser oxide creating a uniform surface for paint application and superior adhesion. Additionally, our media is recycled and regularly replenished to provide a homogenous mixture and consistent surface roughness. The recycling process utilizes a vortex cylinder for filtration which removes the “worn” or light weight particles which is then regularly replaced with new media. This insures our blasted surfaces remain consistent without the fluctuations of “All New” or “Getting Old” media.
Wash Room: 30’x16’x12’ high
Our recirculating high pressure 2-stage wash system utilizes Iron Phosphate to provide efficient removal of manufacturing remnants like oils and mill scale while being environmentally responsible compared to conventional down the drain systems. Once coated, the Iron Phosphate conversion coating will provide superior paint adhesion, impact resistance and improved flexibility. Treated metal surfaces also have the ability to slow the progress of oxidation after being damaged by an external object. By maintaining the chemistry to exacting levels, we insure day to day high performance of your powder coated products.
Powder Application and Recovery Room: 30’x16’x12’ high
Our batch processing allows for total flexibility in painting every imaginable part design without the physical limitations of a dedicated line. From one off parts to mass production, our hanging methods will minimize the witness mark left by the hook and our masking and plugging materials will protect holes and machined surfaces as required. Whether you have a specific color in mind or need to match an existing color, we can meet your needs.
Batch Curing Oven: 30’x16’x12’ high
Our fully programmable 2.5 million BTU batch curing oven with temperature monitoring and air flow mapping provides the power to meet all your part curing needs while providing a repeatable temperature profile. Additionally, the three internal tracks allows for maximum efficiency and maximum loading which translates to less gas usage and reduced cost to you.
Featured Capabilities
- check Blasting removes rust, paint, weld slag, and laser oxide
- check Iron phosphate wash removes oil and manufacturing remnants
- check Iron phosphate conversion coating provides increased adhesion, impact resistance and improved flexibility
- check Batch processing for complete flexibility
- check Repeatable temperature profiles
- check Outdoor dock and crane-accessible indoor dock
Typical Mill Scale, Laser Oxide, and Rust BEFORE Blasting

After Blasting, Surfaces are Clean and Free of Scale, Oxide, and Rust
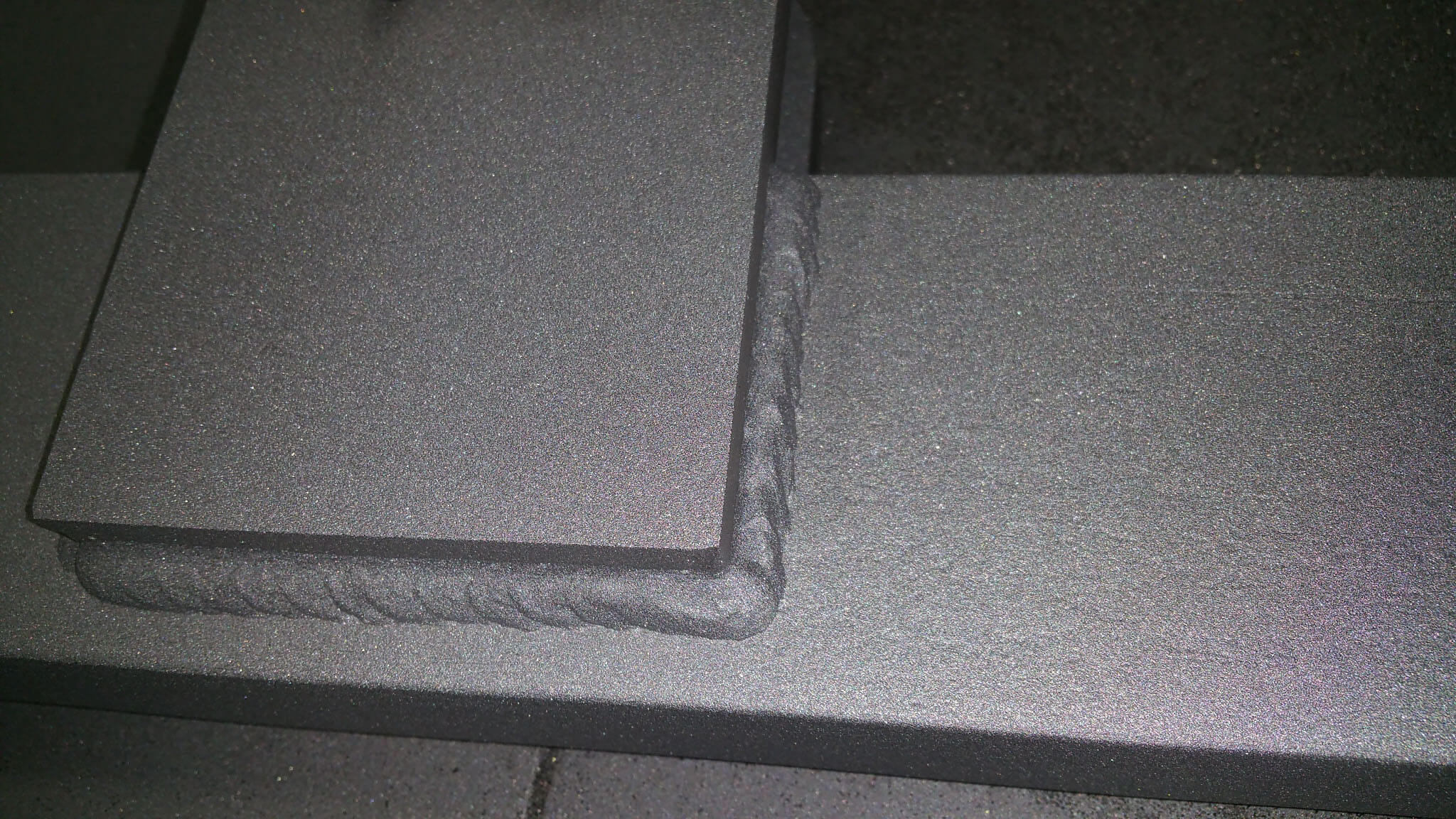